Join the fastest growing community of wholesalers leveraging Thrive's inventory AI platform for dramatic yet painless inventory improvements.
✅ Reduce your dead stock by 80% and improve your fill rates by 8 points.
✅ Optimizes your existing ERP settings.
✅ No need to implement an expensive and disruptive supply chain planning system.
✅ Eliminate the risk of buying technology that may not work for your business.
✅ See the real value of our technology using your data for FREE!
The fastest growing
community of wholesalers
leveraging Thrive's inventory AI platform.
✅ Reduce your dead stock by 80%.
✅ Improve your fill rates by 8 points.
✅ Optimizes your existing ERP settings.
✅ No need to implement an expensive
and disruptive supply chain planning system.
✅ Eliminate the risk of buying
technology that may not work.
✅ See the real value of our
technology using your data for FREE!
Book a Demo
.png?width=2048&height=546&name=Untitled%20design%20(28).png)
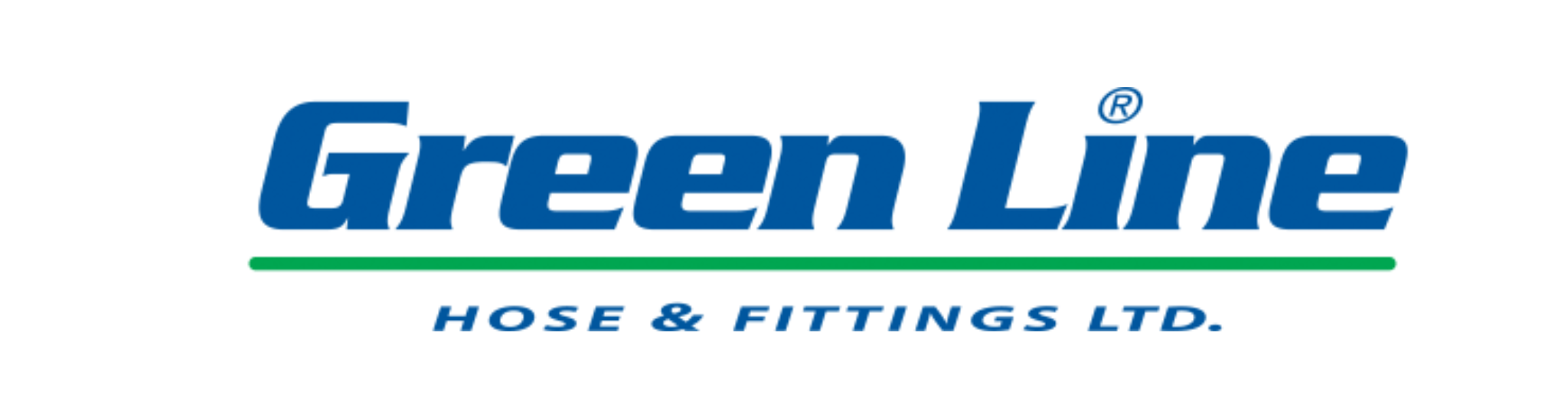
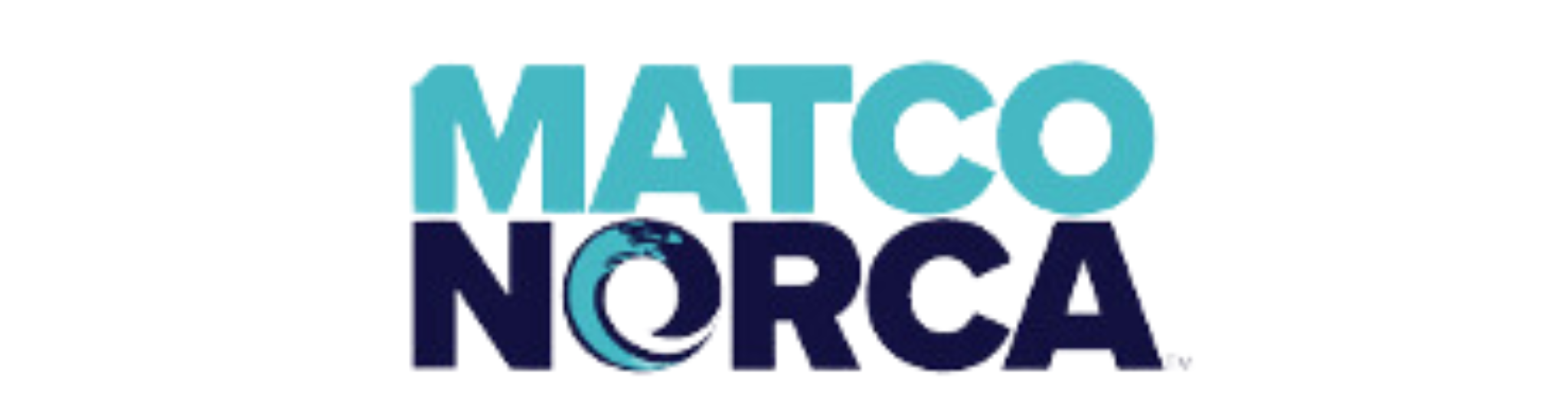
.png?width=2048&height=546&name=Untitled%20design%20(27).png)
"The idea of something being set automatically and the ability to have Thermostock update regularly is very attractive. We've seen the results that it does a better job of keeping track of those C & D items than Eclipse is doing." Katina Mataras, System Analyst, U.S. Electrical
"For our transfer fill rates, we set our goal to equal or greater than 80%. Before Thermostock, it was lower than that regularly. But now, we are consistently at an 88% on our transfer fill rate." Tara Cunningham, Purchasing Manager, General Air
“Twelve months ago, we had a ton of dead stock on our D & E low-selling items. In the last 12 months, we saw a decrease of 78.5% in dead stock on our D & E items. Thermostock is very important." Travis Robinson, National Purchasing Manager, Green Line Host & Fittings
"When someone asks me about Thrive, the first thing I tell people is if your first question is going to be 'Should I do this?' I'll answer it for you – yes. Absolutely. And the second thing is if they ask 'Is it worth the price?' 100% it is." Andrew Yull, Director of Procurement, Johnstone Supply/B&B Trade